Hey you, the person reading this, you can ping engineers or ifls on this thread (if you feel like it)
Previous thread:
https://rdrama.net/h/nerdshit/post/301878/inquiry-into-the-titan-disaster-reveals
Scott Manley video:
Documents:
https://www.news.uscg.mil/News-by-Region/Headquarters/Titan-Submersible/
CliffsNotes:
Oceangate experimented with a full-carbon hull for their submersible, but the hemisphere endcaps would cave in on the models hence the switch to titanium for the final design
The carbon fiber was selected as a cost-cutting material in an effort to make the submersible as light as possible. That in turn was done to save cost on the support ship required to deploy the submersible, as this was intended to become a commercial operation at some point, with submersible expeditions being sold as tours for the general public
Carbon fiber is not on the list of approved materials for the fabrication of human-rated pressure hulls. This is not due to any of its intrinsic properties, but rather due to lack of testing of such vessels.
It is a well known fact that carbon fiber is capable of supporting tensile stress but does not manage compressive stress as well, hence its unsuitability as a material for submersibles. This fact was parroted here a lot by resident subject matter experts
. However, the testifying engineer believes this to not be an issue as the same was said about acrylic plastics, which were initially met with strong skepticism but are now one of the officially approved materials for construction of human-rated pressure vessels. He believes that none of the carbon fiber's downsides are complete deal-breakers and a solution could have been developed that would allow for its eventual implementation. He backs his point by presenting various different composite submersibles, including the chinese Petrel-X that is rated for 10000m depth. He believes that composite materials provide several advantages over traditional ones (like corrosion resistance) and that with enough development and testing carbon fiber could be deployed as a material for pressure vessels, with the issue being that Oceangate did not invest nearly enough in research of this material to justify using it.
Speaking of acrylic, the acrylic window used on the Oceangate vessel was rated only up to a 1000m dive depth, as compared to the nearly 4000m at which Titanic sits. It is a miracle that it hadn't failed, which we know it likely didn't due to analysis of wreckage (see last post)
The reason the window wasn't rated to the correct depth is due to the fact that instead of going for a concave inner surface, like the industry standard, Oceangate instead opted for a filled hemisphere-like shape, with a flat inner surface, with the reasoning being that a concave window would cause lensing and make close-up objects appear further away, which they wanted to avoid for the sake of satisfying the potential customers.
Some information regarding the manufacture process was revealed:
Oceangate had previously constructed 2 prototype vessels, both of which failed, by layering the carbon-fiber sheets only radially. The final design included perpendicular carbon-fiber sheets, which were aligned both radially and longitudinally. It is also revealed that their consultant, Boeing (lmao
) suggested a carbon-fiber sheet to be layered at 45 degrees to radial, but this wasn't done in the final vessel likely due to the difficulty of manufacturing it.
It is also noted that during the construction of the hull, they would notice occasional wrinkling of the carbon fiber in certain spots, which would only accumulate with each subsequent passing and result in a non-smooth cylindrical shape by the end. To combat this, they decided to split the entire 5-inch thick hull into 5 1-inch thick concentric cylinders, each of which would be ground and smoothed at the end to remove said wrinkles and provide a smooth surface for the next layer. The layers would be then held together by some sort of surface-roughener and industrial adhesive. One might imagine that grinding at carbon fiber would compromise its strength, and it is interesting that after taking cross-sections of the 5 different layers and counting the amount of wrinkling sites, they didn't observe any reduction of them and in fact each consecutive layer had more wrinkles than the last, the only difference being that they were invisible from the outside now.
Analysis of the wreckage shows that the hull did fail along the inter-layer seems, though not all layers disjoined in this way, which could either be random chance or an indication that some of the layers were glued together better than others. Similarly there are no signs of carbon-fiber films themselves tearing within each individual layer, which demonstrates that the resin cure which was used between the carbon-fiber sheets held way better than the adhesive which they used to join the bigger layers together
Similarly by analyzing the recovered hull fragments the researchers noted that the imperfect cylindrical shape of the carbon-fiber layers translated into uneven coatings of interlayer adhesive, where some regions would have a lot of adhesive and others would have practically none. In addition to that they also noticed microscopic longitudinal rub marks in between layers and deposits of crushed, powdered glue that would accumulate in some of the voids between the layers. This indicates motion between the different layers which is very very bad as you want the vessel to act as a single solid structure in order to withstand the outside pressure, instead of having these individual sliding layers.
Cross-section analysis of the individual layers also revealed small voids and cavities between the carbon-fiber sheets. Whether this is in any way significant to structural integrity of the bulk material is unknown either to me or the video author.
The frontal metal end-ring which connected the titanium hemisphere to the carbon-fiber hull and was suspected to be the source of initial failure was recovered and analyzed. The suspicions were largely confirmed as inspection of the gluing site which held the ring to the carbon-fiber showed that the glue was peeled right off the metal ring and mostly remained on the carbon-fiber part. (gluing the parts is apparently a industry-standard practice, for more info see last thread). This indicates that the glue-metal interface was likely the source of initial failure. Moreover the video author proposes to narrow it down to the bottom section of the glue-metal interface on the metal end-ring, as that is the segment where the carbon fiber hull was absolutely shredded and no larger pieces remain, as opposed to the upper side where large pieces had stratified into the individual layers discussed above. In his opinion it is the shear motion of the layers around that point which could have destabilized the hull and caused it to be shredded.
The Real-Time Alert System Truth Nuke:
The alert system on the vessel consisted of acoustic sensors mounted around the hull, which would listen for the sounds of shit breaking and record the data for later analysis, and tension sensors, also mounted around the hull, which would measure the tension or compression that the hull underwent and similarly record the data for later. It also seems that not all of the sonic sensors were functioning, but somehow this isn't even the crazy part.
Now, on dive 80, at around 15:30 (shown on graph), during resurfacing the sensors recorder a loud-butt crash. It was so loud that the passengers heard it, it was so loud that potentially the surface crew might have heard it. It was dismissed by Stockton as the carbon hull setting into the metal ring, something unrelated to the structural integrity. But looking at the tension sensor readings at the same time shows a big jump, indicating that the hull had been rapidly deformed.
Looking at the tension sensor readings for subsequent dive 81 (red) and comparing it to previous dive 80 (blue) shows that the vessel behaves differently at the beginning of the dive, indicating that after this bang the hull now has a different deformation mode. And this mode of deformation is localized to the forward-bottom-left area of the carbon fiber, that sits right against the metal end-ring discussed earlier. This behaviour persisted for the following dives as well.
So basically the warning system worked as intended, giving them all the information needed to see that something is going wrong with the vessel, but Stockton chose to ignore it.
The dive 80 happened back in 2022, and since then the submarine was transported, left outside in the weather, fallen off the tow-boat, and dove several more times, all likely worsening its condition, and one engineer even expressed concerns with the matter in which it was lifted by crane, arguing that it wasn't designed for the kind of tension it experiences when being hooked from above and left to dangle.
The TL;DR is that it was literally all willful negligence and they could've stopped and re-evaluated this thing at literally any point right up to the day it sank, but chose not to. What a horrid way to go
Jump in the discussion.
No email address required.
That's cool and all, but are there any pics with their bodies yet?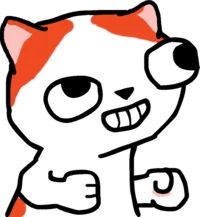
Jump in the discussion.
No email address required.
Here
Jump in the discussion.
No email address required.
More options
Context
I doubt anything is left of their bodies to photograph
Jump in the discussion.
No email address required.
Disappointing but fair
Jump in the discussion.
No email address required.
More options
Context
More options
Context
iirc they recovered some paste with DNA of five different humans. You'd get similar results if you put five dudes into a huge hydraulic cylinder and rammed it with a pressure of 370 bars. Hydraulic press channel can give you ideas about it.
Jump in the discussion.
No email address required.
More options
Context
More options
Context